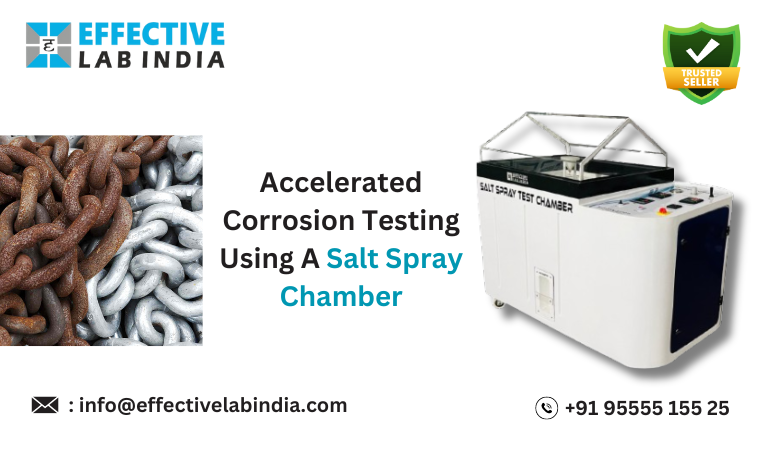
Conducting corrosion tests is essential for ascertaining how durable and long-lasting materials and coatings are. One method that has been proven to be very efficient in carrying out accelerated corrosion testing is the utilization of the Salt Spray Test Chambers. Cyclic Corrosion Test Chambers are another variety that undertakes testing on a more holistic scale by replicating actual external weather conditions. This post discusses the processes, advantages, and uses of these important testing techniques.
Understanding Corrosion and Its Impact
What is Corrosion?
In their environment, chemical reactions typically lead to corrosion in the case of materials, usually metals. As time passes by, this situation affects how strong or efficient the materials are hence creating numerous problems in different sectors.
Effects of Corrosion on Materials and Industries
Structural failures, safety hazards, and significant financial losses are all simply because of corrosion. Companies that are in automotive, aerospace, construction, and electronics are affected more by the effects of corrosion than any other industry, hence the need for proper testing and prevention measures.”
Overview of Corrosion Testing Methods
Traditional Corrosion Testing Methods
Some things are done by traditional methods like natural weathering or field testing…they are slow and sometimes impossible amidst fast-moving industrial settings although they are correct.
Modern Accelerated Corrosion Testing Methods
Contemporary processes like Salt Spray Testing and Cyclic Corrosion Testing allow for controlled, accelerated evaluation of corrosion resistance by providing faster, more precise results.
Salt Spray Test Chambers
Definition and Purpose
Salt Spray Test Chambers are enclosed units, specifically constructed to mimic a salty mist for a highly corrosive climate These chambers test the corrosion of different components, such as material, protective VH coatings, and paint, offering essential facts on longevity.
Historical Development
Over the past many years, the assessment of corrosion through the use of salt spray has been a central technique whose variations have been in line with technology improvements that guarantee better and more reliable results Lorem ipsum.
How Salt Spray Testing Works
Components of a Salt Spray Chamber
A cabinet is part of a) a) the Salt Spray Chamber, found in most examples, and a saline solution reservoir, sprayers, as well as temperature and humidity regulation systems being others.
Testing Procedure and Parameters
To ensure the same conditions, controlling like humidity must be done, as well as pH and temperature. This saline mist test has three stages: first preparing 5% NaCl solution, secondly putting the sample into the chamber; and third exposing it to saline mist.
Key Parameters in Salt Spray Testing
Salt Solution Concentration
In a standard 5% solution of NaCl, the concentrations may, however, be altered to suit specific testing needs
Temperature and Humidity Control
The chamber is often kept at 35°C (95°F) and with high humidity to promote rapid rusting.
pH Levels
The pH of saltwater is typically kept between 8.3 and 8.2 as in the natural sea water.
Duration of Exposure
“Depending on the projection of expected performance for the material and the general standards within that industry, the exposure time can vary from 24 to several thousand hours.”
Advantages of Salt Spray Testing
Rapid Results
We offer fast results through salt spray testing which replicates years of natural corrosion in just days or weeks.
Cost-Effectiveness
Salt Spray Chambers help to reduce the cost of time-consuming field testing by speeding up the testing process.
Consistency and Reliability
It is such a dependable method in quality control, due to the fact that it can be repeated and trusted, thanks to stable test conditions.
Applications of Salt Spray Testing
Automotive Industry
The purpose of salt spray testing is to see if these parts can last when exposed to various elements like sea salt which is very corrosive and even acids.
Aerospace Sector
It is testing materials used in airplanes to ensure safety and durability under harsh atmospheric conditions.
Construction Materials
It assesses how long building materials last in moisture-laden or coastal areas.
Electronics and Consumer Goods
Ensures that products can withstand severe conditions without experiencing any failure
Cyclic Corrosion Test Chambers
Definition and Purpose
The Cyclic Corrosion Test Chambers are designed to replicate real-word environmental conditions by going through various climates, offering a more extensive appraisal of the ability of a material to resist corrosion.
Comparison with Salt Spray Test Chambers
While Cyclic Corrosion Chambers imitate very different climates to give more real ways of evaluating material performance over time, Salt Spray Chambers give constant saline conditions.
How Cyclic Corrosion Testing Works
Components and Features
Cyclic Corrosion Chambers come with multiple climate settings, advanced monitoring systems, and programmable controllers to imitate different environment conditions.”
Testing Procedure and Parameters
To mimic actual-life rust processes, samples undergo numerous cycles that consist of a spray of salty water, high moisture levels as well as desiccation.
Benefits of Cyclic Corrosion Testing
Realistic Simulation of Environmental Conditions
Cyclic Corrosion Testing is a process that imitates the various weather conditions to establish more accurate material performance predictions.
Enhanced Predictive Accuracy
Among the reasons why this method is better in high-stakes industries like automotive and aerospace is that it provides more information on how materials under real-world conditions will act.
Applications of Cyclic Corrosion Testing
Automotive Industry
To guarantee that the durability of car parts in different environmental conditions is maintained, it is necessary for Cyclic Corrosion Testing to be carried out.
Marine Industry
Examine the endurance of materials and coatings employed in marine surroundings that are highly corrosive.
Industrial Coatings
Assesses how well protective coatings behave when they are used in different types of industries.
Selecting the Right Corrosion Test Chamber
Factors to Consider
When you are selecting a corrosion test chamber, take into consideration factors such as adherence to global standards, chamber dimensions, simplicity in utilization as well as maintenance needs.
Importance of Compliance with Standards
Make sure that the equipment has met standards like ASTM B117 plus ISO 9227 for precision as well as dependability.
Top Manufacturers of Corrosion Test Chambers in India
Effective Lab India
Effective Lab India is located in Mumbai and makes varied salt spray chambers as well as cyclic corrosion test chambers up to global standards. Its items are admired for their attention to detail and enduring nature.
Conclusion
Industries that need materials and coatings with high longevity and reliability consider accelerated corrosion testing involving cycled corrosion test chambers and salt spray as crucial. Manufacturers benefit from such approaches that provide speed, cost containment, and reliability enabling them to predict accurately how long their products will be useful. The world-class electrochemical testing solutions such as those offered by top Indian manufacturers include EFFECTIVE LAB INDIA, Effective Lab Equipment, Ascott Analytical, and Advance Equipments.